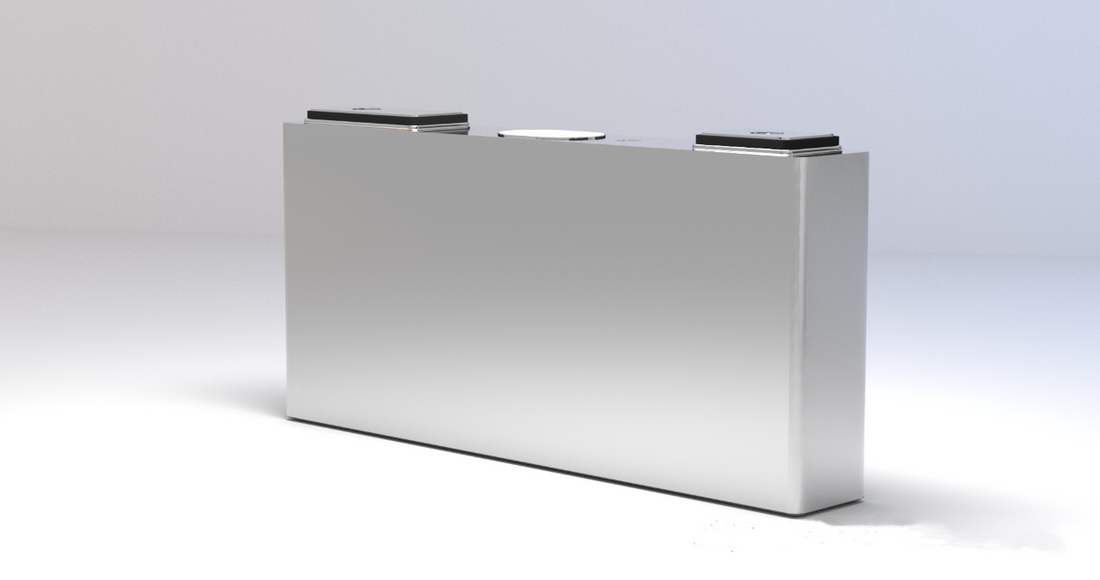
Why are aluminum shells used for lithium batteries?
1.Lightweight:
- Low density: The density of aluminum is about 2.7 g/cm³, significantly lower than that of steel (around 7.8 g/cm³). In electronic devices (such as mobile phones and laptops) and electric vehicles that pursue high energy density and lightweight designs, aluminum shells effectively reduce overall weight, improving battery life.
2.Corrosion Resistance:
- High-pressure environment adaptability: The positive electrode materials of lithium batteries (such as ternary materials, lithium cobalt oxide) operate at high voltages (3.0-4.5V). Under this voltage, aluminum forms a dense aluminum oxide (Al₂O₃) passivation film on its surface, preventing further corrosion. In contrast, steel is prone to corrosion from electrolytes under high pressure, which can degrade battery performance or cause leakage.
- Electrolyte compatibility: Aluminum shows good chemical stability with organic electrolytes (such as LiPF₆), making it less likely to react over prolonged use.
3.Conductivity and Structural Design:
- Current collector connection: Aluminum is the preferred material for the positive electrode current collector (such as aluminum foil). The aluminum shell can directly connect to the positive electrode, simplifying the internal structure, reducing resistance, and improving energy transfer efficiency.
- Conductivity needs of the shell: In some battery designs, the aluminum shell serves as part of the current path (such as in cylindrical batteries), requiring both conductivity and protective functions.
4.Manufacturing Performance:
- Excellent ductility: Aluminum is easy to stamp and stretch into shape, making it suitable for mass production of complex shapes (such as square and soft-pack aluminum-plastic films). Steel shells, on the other hand, are more difficult to process and costlier.
- Sealing assurance: Aluminum welding technology (such as laser welding) is mature, effectively sealing the electrolyte and preventing moisture and oxygen intrusion, which helps prolong battery life.
5.Thermal Management:
- High heat dissipation efficiency: The thermal conductivity of aluminum (about 237 W/m·K) is much higher than that of steel (around 50 W/m·K), which helps the battery dissipate heat quickly during operation, reducing the risk of thermal runaway.
6.Cost and Economics:
- Material and processing costs: Aluminum is relatively affordable as a raw material and has low processing energy consumption, making it suitable for mass production. In comparison, materials like stainless steel are more expensive.
7.Safety Design:
- Pressure relief mechanism: Aluminum shells can be designed with safety valves (such as the CID (Current Interrupt Device) reversal structure in cylindrical batteries) to release internal pressure during overcharging or thermal runaway, preventing explosions.
8.Industry Practice and Standardization:
- Aluminum shells have been widely used since the early commercialization of lithium batteries (such as Sony's 18650 battery released in 1991), leading to the establishment of a mature industrial chain and technological standards, further solidifying its mainstream position.
9.Exceptions:
- In some special cases, steel shells are used: for example, in applications that require extremely high mechanical strength (such as certain power batteries or extreme environmental applications), nickel-plated steel shells may be chosen, though this comes at the cost of increased weight and expense.
Summary: With its comprehensive advantages of being lightweight, corrosion-resistant, highly conductive, easy to process, effective in heat dissipation, and cost-effective, aluminum has become the ideal choice for lithium battery enclosures, perfectly balancing performance, safety, and economic needs.