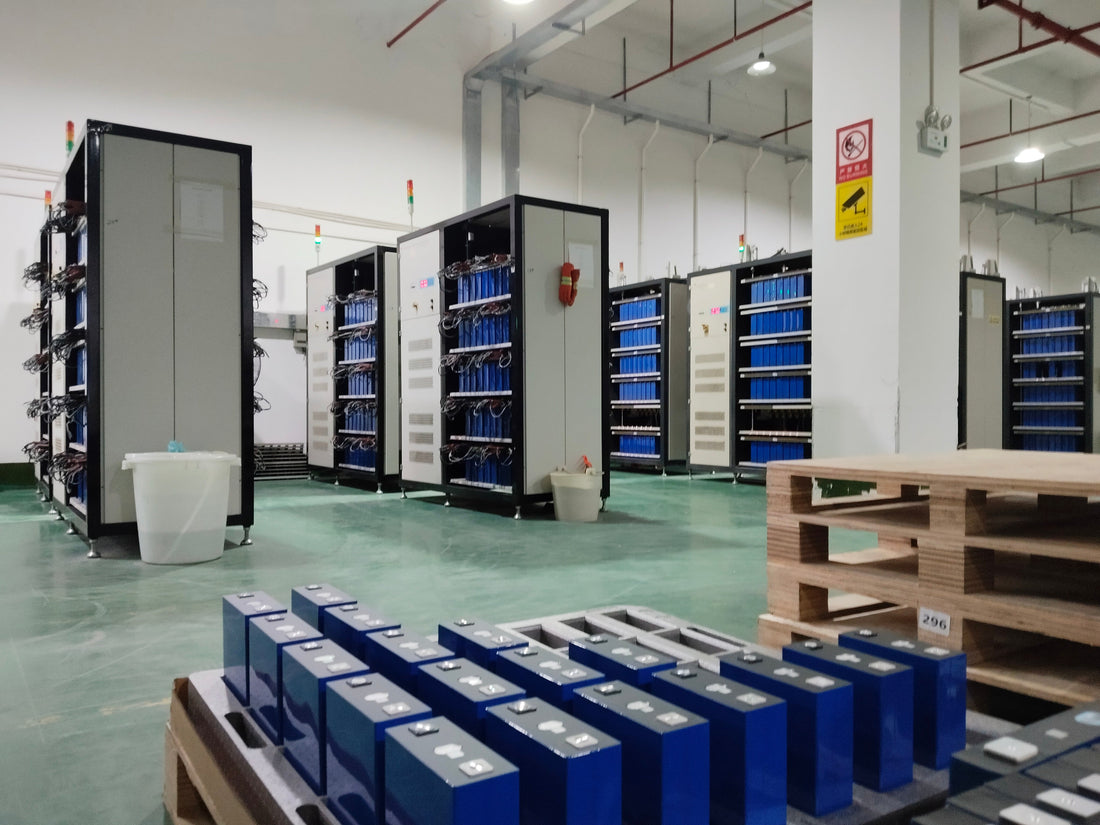
Why do battery cells need to undergo aging tests?
The lithium battery cells need to undergo aging treatment after manufacturing, which is a key step in the battery production process. The purpose is to stabilize the internal chemical and physical states of the cell by leaving it idle under specific environmental conditions (such as temperature and time), ensuring its performance, safety, and consistency. The following are the main reasons and functions of cell aging:
I. Core Purpose of Aging:
-
Stabilize SEI Film (Solid Electrolyte Interphase)
After the initial charge-discharge (formation), an SEI film forms on the anode surface, but its structure is initially unstable. During the aging process, the SEI film gradually improves and passivates, reducing side reactions (such as electrolyte decomposition) in subsequent cycles and improving cycle life. -
Release Internal Stress
After the cell is wound/stacked and electrolyte is injected, internal materials (such as electrodes and separators) may generate stress due to mechanical deformation or uneven electrolyte infiltration. The aging process allows the stress to be released slowly by keeping the cell idle, avoiding issues like separator wrinkles or micro short circuits due to concentrated stress. -
Release Gases
A small amount of gas (e.g., CO₂, H₂) may be generated during the formation and electrolyte injection process. During aging, gases are accelerated to escape through idle time or a high-temperature environment, preventing the cell from swelling or poor interface contact. -
Defect Screening
During aging, the cell's voltage, internal resistance, and self-discharge rate are monitored to identify abnormal cells (such as micro short circuits or electrolyte leakage), ensuring defective products do not enter subsequent processes. -
Balance Electrolyte Distribution
After electrolyte injection, it needs to sufficiently infiltrate the electrode and separator pores. Aging provides time for the electrolyte to distribute evenly, reducing local dry spots and improving ion transport efficiency.
II. Specific Forms of Aging Process
Note: After formation, cells are tested for OCV (Open Circuit Voltage) and ACIR (Alternating Current Internal Resistance) before and after aging, and the K-value of the cell is calculated using these.
-
Room Temperature Aging (Idle at room temperature)
Conditions: Static at 25-30°C for 24-72 hours.
Purpose: Initially stabilize the SEI film, release mechanical stress, and expel gases. -
High Temperature Aging (Accelerated Aging)
Conditions: Static at 45-60°C for 12-48 hours.
Purpose: Accelerate the stabilization of the SEI film and gas expulsion, shorten production cycles, and is commonly used for high energy density or thick electrode cells. -
Charge-Discharge Cycle Aging
Conditions: Perform 1-3 small current charge-discharge cycles.
Purpose: Further activate the electrode materials, optimize interface contact, and check capacity consistency.
III. Effects of Aging on Cell Performance
-
Improves Cycle Life
A stable SEI film reduces active lithium loss and electrolyte decomposition, delaying capacity degradation. -
Reduces Self-Discharge Rate
Aging screens out cells with high self-discharge rates (e.g., voltage drop >5mV/day), preventing thermal runaway caused by variations in individual cells in a battery pack. -
Improves Safety
Expelling gases and releasing stress can reduce the risk of cell swelling, internal short circuits, and lower the probability of thermal runaway. -
Improves Consistency
After aging, the voltage and internal resistance distribution of cells become more concentrated, benefiting battery pack matching and balancing management.
IV. Risks of Insufficient Aging
If aging time is omitted or shortened, the following may occur:
-
Unstable SEI Film:
Continual electrolyte consumption during cycling, leading to capacity drop. -
Gas Residue:
The cell may swell, posing safety hazards (e.g., liquid leakage in pouch cells). -
Undetected Micro Short Circuits:
Localized heating after grouping, which may accelerate aging or even cause thermal runaway. -
Uneven Electrolyte Infiltration:
Increased polarization, resulting in reduced rate performance.
V. Optimization Directions for Aging
-
Dynamic Aging Monitoring
Use online monitoring systems (e.g., voltage, temperature, pressure sensors) to track the aging process in real-time. -
Gradient Temperature Control
Adjust the temperature in stages (e.g., first accelerate gas expulsion at high temperature, then stabilize the SEI film at room temperature). -
Materials and Process Improvement
Optimize electrolyte formulas (e.g., adding film-forming additives) or pre-lithiation processes to shorten aging time.
Conclusion:
Aging is a crucial step in balancing production efficiency and product quality. By adjusting time, temperature, and environmental conditions, the reliability, safety, and lifespan of lithium batteries can be significantly improved. Different systems (e.g., lithium iron phosphate vs. ternary) and forms (cylindrical/square/pouch) of cells require targeted aging processes to achieve optimal performance.